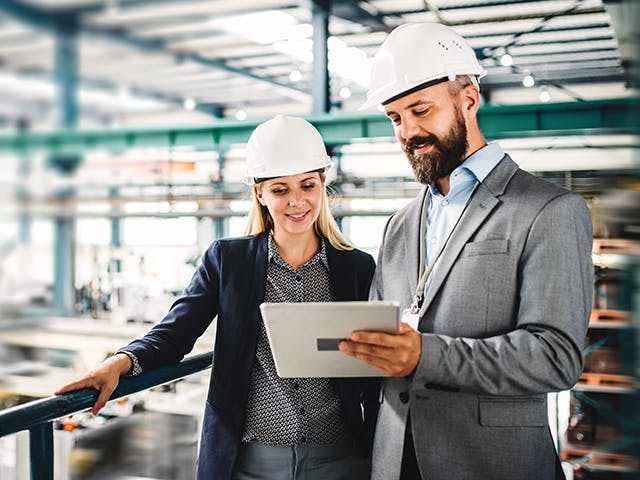
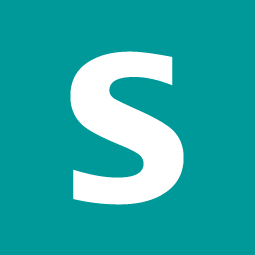
Opcenter APS software can be used for long-term strategic planning (months and years), medium-term tactical planning (weeks), and for detailed sequencing and scheduling.
Detect bottlenecks, reduce setup time. Increase machines and tools utilization. Reduce work in progress.
Reduce waste. Easily identify shortages. Optimize material flow and production synchronization.
Increase availability and efficiency. Reduce lead time. Improve adherence to projections.
Company:Natural One
Industry:Consumer products & retail
Location:Sao Paulo, Brazil
Siemens Software:Opcenter APS
Accurate predictions help you meet production demand, keep low stock levels and high utilization. Flexibility helps you alter plans to fulfill last minute requests.
Quickly answer customer requests and keep clients happy without losing control of planning. Know how to balance and prioritize production capacity and constraints.
Keep control of costs and understand how planning changes impact efficiency and stocks. Understand how new assets and resources will influence production figures.
Opcenter APS provides customizable product planning and scheduling. It increases resource use and on-time delivery, reducing inventory and waste.
Instantly, securely and easily collaborate with colleagues, partners and customers with Siemens’ next-generation, cloud-based collaboration solution, Teamcenter Share.